Lube Matters
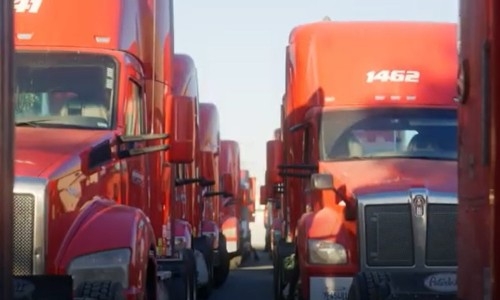
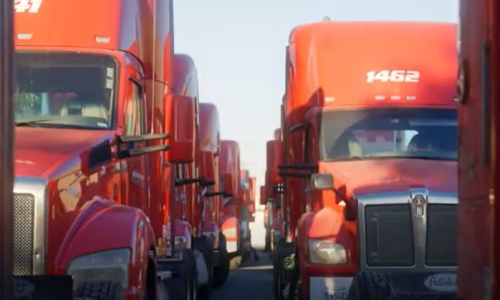
It’s the preferred oil for their entire fleet
Ecology Transportation Sees Dramatic Results
with Chevron Delo® 600 ADF
By Zach Sutton
Stay in the loop and receive our weekly blog articles.
Sign up to receive our weekly blog articles
Thank you!
Oops! Something went wrong.