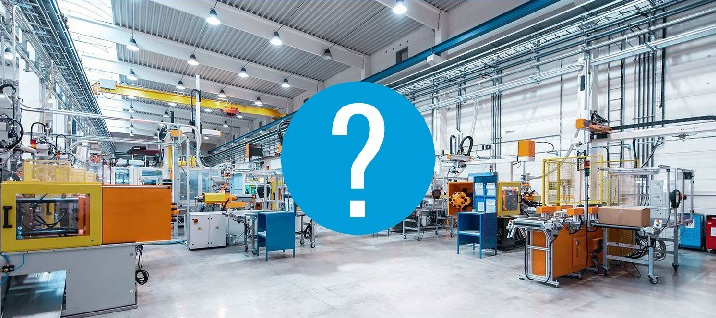
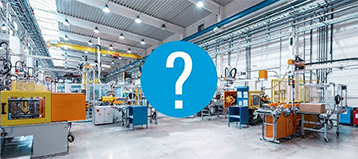
Industrial Products FAQs
Compressor Oils
A: Cetus PAO is formulated with a PAO or Group IV base oil, while HiPerSYN is formulated with Group III base oil.
A: It depends on the type and percentage of gas that comes in contact with the lubricant.
A: The switch can be made only if the seals are changed. Diester-based oils swell seals, whereas, petroleum oils do not. So, if the seals are not changed when the oils are changed, the equipment would leak after the change-out.
A: No, PAG oils are highly incompatible with non-PAG lubricants. We suggest using Cetus EliteSyn NG as a PAG based compressor oil. Your Chevron representative will be glad to work with you to determine the exact product recommendation for your application.
Gear Oils
A: Typically, foaming occurs because the anti-foam depressant additive has depleted. When is the last time your oil has been changed? Foaming can also be the result of water contamination, or overfilling the gear box, to name a few root causes.
Hydraulic oils
A: While hydraulic oil standards are commonly agreed to and well established, the relative performance of hydraulic oil varies. This is due to variations in approaches and experience in formulating products, variations in the base oils used (hydraulic oils are in excess of 98 percent base oil) and different target applications and performance. Additionally, there are hydraulic oils that emulsify water, and those that demulsify water. Demulsifying and emulsifying hydraulic oils are typically not compatible due to the nature of their chemistries. For the purpose of this FAQ, we are addressing demulsifying hydraulic oils.
A: Variations in the base oil and performance additives used are the primary differences in hydraulic oils. To manage costs, some lubricants manufacturers use a variety of base oils and additives. This can lead to performance differences in these areas: oxidation, water handling ability, sludge formation, filter life, productivity, fuel efficiency, anti-wear/extreme pressure (EP), cold temperature pumpability. Consistent performance standards are important to help ensure risk-free equipment operation, and higher quality hydraulic oils meet or exceed these standards. The use of different types of performance additives in the formulation can make a big difference. The approaches can vary, including the use of more or less zinc (an element in a key anti-wear additive), or the use of no zinc at all, such as in ashless hydraulic oils
A: Variations in the base oil and performance additives used are the primary differences in hydraulic oils. To manage costs, some lubricants manufacturers use a variety of base oils and additives. This can lead to performance differences in these areas: oxidation, water handling ability, sludge formation, filter life, productivity, fuel efficiency, anti-wear/extreme pressure (EP), cold temperature pumpability. Consistent performance standards are important to help ensure risk-free equipment operation, and higher quality hydraulic oils meet or exceed these standards.The use of different types of performance additives in the formulation can make a big difference. The approaches can vary, including the use of more or less zinc (an element in a key anti-wear additive), or the use of no zinc at all, such as in ashless hydraulic oils
A: OEMs are very specific about the quality of lubricant used in their equipment and for very good reason. If the lubricant fails, so does their equipment. It is important to follow OEM guidance for warranty and for the extended life of your equipment. Off-highway emission standards are becoming stricter—leading to a need to improve fuel efficiency. In mobile equipment such as excavators, fuel economy is linked to engine performance and hydraulic system efficiencies. By improving hydraulic system efficiencies, equipment can use less fuel per hour and increase production per hour—leading to improved utilization. Hydraulic system pressures are also increasing, thus resulting in higher operating temperatures, which causes increased demands on the hydraulic fluids. In combination with these systems-related demands, equipment builders are moving to extended service intervals for fluids. Due to higher hydraulic system pressures and the need for extended service life, OEM recommendations are moving to higher performance products.
A: Hydraulic oil AW is made from Group I oil (currently Hydraulic Oil AW in North America is mostly made with Group II base stocks), Rando HD is a straight grade and Rando HDZ is a high viscosity index (‘multi-grade’) lubricant made from Group II base oils. Rando HDZ 32, 46 and 68 viscosity grade oils are approved by major pump manufacturers. The high viscosity index can provide minimal viscosity change over a wide range of operating temperatures.Fast water separation and excellent filterability ensure the product performs well in systems with close tolerances. Rando HDZ hydraulic oil also provides excellent oxidation stability at high operating temperatures, potentially allowing for extended service life and cleaner performance.
A: One way of comparing the oxidation performance of different oils is through a laboratory test called the TOST test where the results are given in hours. This test has a relationship to the performance capability in field applications. Actual life of the oil in an actual hydraulic system will depend on the operating environment. The products that have historically been called hydraulic oils would generally meet a TOST life of around 1,500 hours or less. We call this the ‘industry standard.’ Rando® HDZ provides a TOST life of more than 5,000 hours, thus three times the ‘industry standard.’ Clarity® Synthetic Hydraulic Oil AW provides a TOST life in excess of 10,000 hours, thus, six times the life of an industry standard product. TOST testing, while not the only measure of hydraulic oil performance, does show a good correlation to relative oil life in field use.
A: If you are currently using Rando HDZ, you do not have to flush before using the new and improved Rando HDZ. If you are currently using an emulsifying hydraulic oil, you will have to drain, change filters, flush and fill with our demulsifying hydraulic oils due to incompatibility. If you are not aware of the properties of the in-use hydraulic oil, then drain, change filters, flush and fill with our hydraulic oil. If you intend to use a Clarity® (ashless/zinc-free) hydraulic oil where previously an oil containing zinc had been used, then a drain, filter change, flush and refill is required. Zinc and non-zinc formulations are often not compatible. Generally, there is no need to drain and refill products when products are fully compatible, however, to maximize performance, tanks must be drained, filters changed and tanks refilled with the new, clean product to receive the full benefit of the new, clean product. We always recommend following OEM recommendations and keeping the filtration, hoses, breathers and seals in good condition to ensure optimum performance.
A: Oils do oxidize over time, in hydraulic and circulating systems; a sample of the oil should be taken every 6 months or annually to determine condition.
A: Yes, all our hydraulic oils would have an antifoam additive.
A: Rando HDZ provides improved shear stability performance, with the use of a new viscosity index improver. Since the correct viscosity is maintained over a wider temperature range, pump efficiencies result. These efficiencies often can manifest themselves in lower pump temperatures and potentially extending the life of the pump and oil. There are a number of factors that impact drain interval decisions. Some of these are operating conditions, system cleanliness, OEM drain recommendations, etc. In general, Rando HDZ, along with a used oil analysis program like LubeWatch® can provide the best product / program combination to help a customer determine how far they can actually extend their drain intervals safely.
A: FZG is a test normally reserved for gear oils to measure gear performance. It is a test reflective of combined EP/ AW performance in gear sets. Some companies include the FZG result in published data. Some hydraulic oil products with gear performance can indeed be used in lightly loaded gearboxes, but often their use is limited to smaller high-speed gearboxes because of the lower viscosities used in hydraulic oils. FZG results are given on a scale of 1-12 with 12 being the highest performance. For example, Clarity® Hydraulic Oil AW 32, 46, 68 has an FZG rating of ≥ 12, whereas, Rando HDZ 32 has a rating of ≥ 11, and Rando HDZ 46, 68, 100 have a rating of ≥ 12.
A: For many years Zinc Dithiophosphate (ZDDP), a metallic additive has been used in hydraulic oils as an approach to provide good anti-wear performance. The anti-wear performance of the ZDDP has been shown to give good protection in vane type pumps where vane tip wear was problematic. The use of ZDDP, however, does have its challenges, most notably with both the performance in the presence of water and contributing to degradation of metals, most notably that in piston pumps. There are a number of factors that impact drain interval decisions. Some of these are operating conditions, system cleanliness, OEM drain recommendations, etc.
A: It depends on type & percentage of gas coming into contact with the lubricant.
A: The switch can be made only if the seals are changed. Diester-based oils swell seals, whereas, petroleum oils do not. So, if the seals are not changed when the oils are changed, the equipment would leak after the change-out. Modern formulations have improved in this area and continue to meet industry requirements. Specially designed premium hydraulic oils that do not contain Zinc have demonstrable advantages in these areas. Chevron ashless hydraulic oils, such as Clarity hydraulic oil AW and Clarity Synthetic hydraulic oil AW can be used in both vane and piston pumps.
A: Properly formulated ashless formulations have a high FZG rating making them suitable for light gear service. Also, the technology employs base oils with a higher viscosity index. This improves low-temperature start performance and better film thickness at elevated temperatures. This can provide an opportunity to rationalize the number of products in use at a certain location while improving pump efficiency.
A: No, we do not make a fire-resistant product.
A: No, Clarity hydraulic oils utilize acidic additives, many other AW hydraulic oils utilize alkaline additives, so they are not compatible.
A: 1000 THF is a multi-grade 10W30 viscosity oil.
A: AW Hydraulic Oils are designed for system with pressures over 1,000 PSI.
A: AW Hydraulic Oils are designed for system with pressures over 1,000 PSI.
A: If you have a hydraulic oil in the system, do not add GST since it is not compatible with common AW hydraulic oils.
A: Rando® HDZ 32 or 46 has a dielectric strength of 35 KV. Drain, flush, and refill. We do not make an EDM fluid which is a true 100% non-conductive oil.
A: No, Caterpillar requires a product that contains 900 ppm zinc. We recommend Delo® TorqForce SAE 10W.
A: 303 is an obsolete John Deere recommendation, 1000 THF is a good option.
A: Chevron 1000 THF is recommended for this specification.
A: No, we do not make a product that meets this requirement.
Industrial greases
A: Chevron does not have any low-temp/low viscosity (below ISO 100) in our grease product line.
A: No, they are not. We recommend purging each time you change out any grease.
A: NLGI 00 are semi-fluid, pourable products. NLGI 2 greases are not pourable & much more consistent.
Specialty oils
A: GST® 32 or Aries® 32 or Regal R&O
A: If the maximum bulk temperature does not exceed 550°F, then we recommend Heat Transfer Oil Grade 46.
A: Way Lubricant Vistac has an emulsifier which helps keep it on the slides and ways of machine tools. It also hold water in suspension. Way Lubricant separates from water and separates more quickly from water containing metal working fluids.
A: Soluble Oil B.