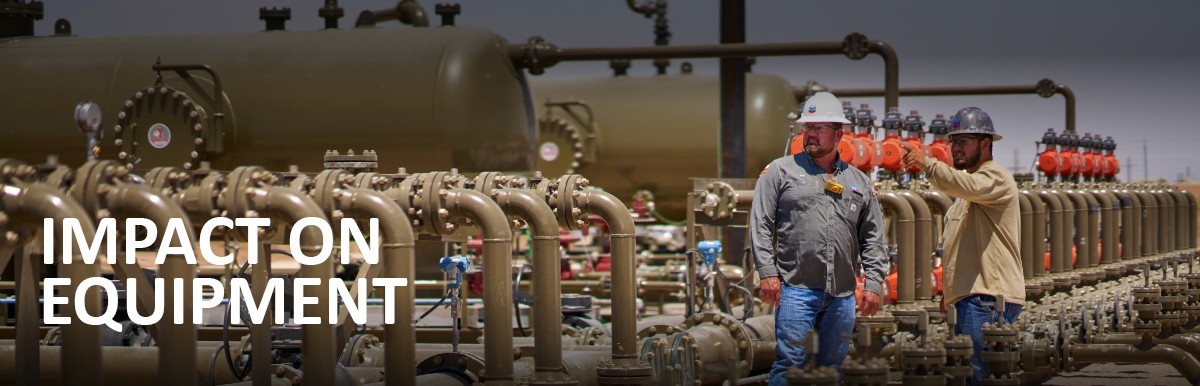
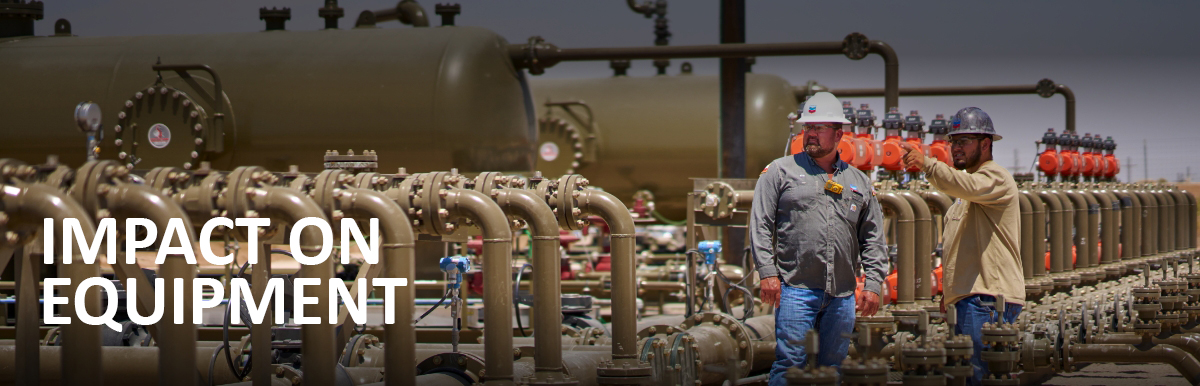
INDUSTRIAL LUBRICANT LEARNING CENTER
_____________________________________________________
OPERATIONAL CHALLENGES EQUIPMENT IMPACT SOLUTIONS
GAS GATHERING & COMPRESSION
Protect your productivity
When equipment is continually producing or delivering a product, downtime brings business to halt. Unplanned maintenance and unexpected repairs impact more than your budget. These are some of the conditions that can develop inside your engines and the critical parts affected:
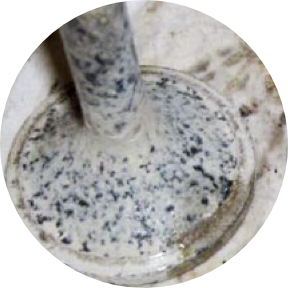
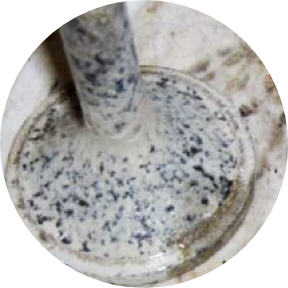
Valve wear/recession
- Valve pounds back into the cylinder head (recedes) due to the repeated closing action. Improper valve seating causes rough operation, power loss, reduced fuel economy and increased emissions
- Occurs at the valve seat interface
- Caused by metal abrasion, high-temperature corrosion, frictional sliding and adhesion
Impact on equipment: If not corrected, valve recession requires a cylinder head overhaul

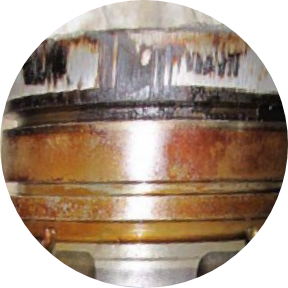
Piston deposits
- Prevents rings from rotating/providing sufficient sealing of combustion gases
- Significant liner wear with high heat and repeated contact
- Compromised rings allow oil to enter exhaust system, clogging filters and straining emission control systems
Impact on equipment: If not corrected, deposits create excessive wear and inhibit the performance of pistons, valves, spark plugs and other systems which can lead to failure.
The Damaging Effects of Derating
When operating at low load, gas engines may not have enough cylinder pressure to maintain oil control. This allows oil to get past combustion chamber rings and create ash deposits. Extended operation at low loads can also lead to the buildup of deposits on valves, spark plugs and piston rings.
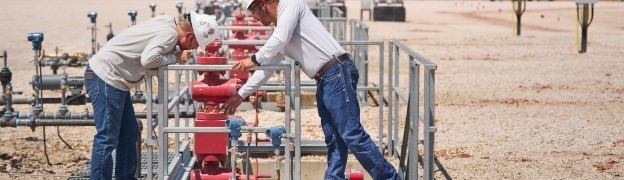
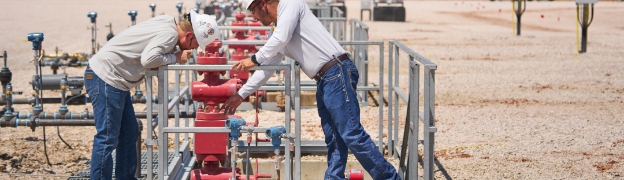
Are maintenance practices compromising
your equipment’s performance?
Set Schedules
Following a set schedule for engine oil changes ignores the condition of oil or equipment. As a result,
companies often change oil before it’s necessary and miss early signs of equipment damage that would
be detected with lubricant monitoring.
Slip Streaming/Sweetening
This common practice offers some initial upfront savings by extending oil drain intervals and allowing operators to purchase and stock one product. However, drawing used oil from the engine and feeding it into the compressor dilutes the levels of wear metals and other contaminants, masking problems that could be occurring in the engine. As wear-causing deposits remain in the engine longer, they have more time to accumulate, circulate and cause damage.