Let’s Filter New Lubricants
ISOCLEAN Your Way to Clean
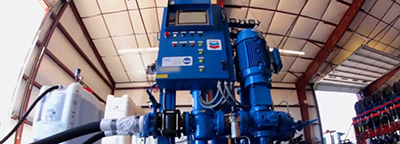
As we pointed out in an earlier article, just because a lubricant is new does not mean it is clean. In fact, right out of the container, your new oil more than likely does not meet the equipment manufacturer’s ISO cleanliness specifications. Many equipment operators seek to compensate for this by putting new oil through a filtration system, but systems and methods vary widely. Which then raises the question: can you simply use an oil filter to get to the required ISO cleanliness code?
The short answer: It’s not that easy.
Going to a tight micron rating or beta ratio on an oil filter can be very detrimental to the finished lubricant by removing additive components necessary to the proper performance of the oil. Moreover, lubricants from different suppliers may meet the same performance OEM specifications on paper, but their specific formulations to meet those specifications can be very different. Even the base oil selection in a finished lubricant will have an effect on the filtration of the final lubricant formulation and its additives.
For instance, polydimethylsiloxanes and other silicone foam inhibitors or defoamers can be from 1 to 10 microns (or larger) in size. They are a common choice in many lubricant formulations, especially engine oils. But what happens when they’ve been sitting in an unused engine oil for 1.5 years? The foam inhibitors can group together and form larger particles as the oil sits in storage. The size, however, is less of a factor than their tendency, as a surface-active additive, to bead up and get trapped on the surface of the filter media.
Figure 1 shows a fresh new sample of heavy-duty engine oil that was filtered at three microns with a beta of 1,000 micro glass filter media. After nine passes through the filter element, the filter pulled out a significant amount of foam inhibitor, which can be seen on the filter element using a scanning electron microscope (SEM) and special lighting techniques. In other words, this lubricant has been over filtered to a point that the foam inhibitor will lose effectiveness.
Here’s the problem: under-filtering a lubricant means it will likely not be clean, but over-filtering the lubricant means it may not function as it was designed. So how do you know when and where to start filtering your fresh lubricant? The filter provider can’t tell you – they have no idea what makes up the lubricant formulation. The lubricant manufacturer can be a good source, since they know what is in the lubricant, but only if they have performed filtration testing and set a procedure for the specific lubricant and viscosity grade. If they have not done that work, their answers are just guesses.
In the defoamer example cited earlier, you certainly could run the ASTM D892 analytical foam testing and see if it passes. But what if you removed 50% of the foam inhibitor from the lubricant when you filtered it? It still may pass the D892 test initially, but what happens after a few hours of operation with that lubricant? Will there be enough foam inhibitor to last until the intended service interval of the lubricant?
The foam inhibitor is just one of many soft particles in a lubricant that may be counted in a particle counter, but is needed to stay in the lubricant. Tight filtration runs the risk of filtering out essential additives such as corrosion inhibitors, demulsifiers, anti-wear or extreme pressure additives, and more.
Bottom line – proper filtration is a science, just as much as lubricant formulation. An easier way to get clean lubricants is to buy them clean from the lubricant marketer. However, many marketers just buy a filtration skid and filter a lubricant just as any customer would, with no proven guidance from the lubricant manufacturer. And different marketers are likely to have different filtration methods and procedures for the same product, with no oversight on the product’s integrity after filtration. That’s risky business.
The Chevron ISOCLEAN® Certified Lubricants Program is different from any other lubricant manufacturer’s cleanliness assurance process because the oil company is standing behind it. The program and participating ISOCLEAN Approved marketers follow a strict filtration process that has been tested, approved and proven to work at Chevron’s Richmond Technical Center in Richmond, California.
All lubricant marketers participating in the ISOCLEAN program use the exact same customized filtration skid and a proven filtration process that is specific to each unique lubricant formulation and viscosity grade. Also, specific testing is conducted on each ISOCLEAN Certified batch to assure the product meets customers’ and Chevron’s expectations. Chevron has done all the filtration work in a laboratory on every product line offered under the ISOCLEAN Certified program. Each product is backed by Chevron lubricant formulators and Chevron Lubricants Company for filtration cleanliness and product integrity after filtration. We stand behind ISOCLEAN filtration because we developed the science to safely and effectively filter our finished lubricants. You can rest assured that the Chevron ISOCLEAN Certified Lubricants meet all OEM specifications for viscosity, performance and cleanliness.
03/31/2020