Understanding Ultra-Low Ash Lubrication Technology
How we minimize ash without sacrificing performance
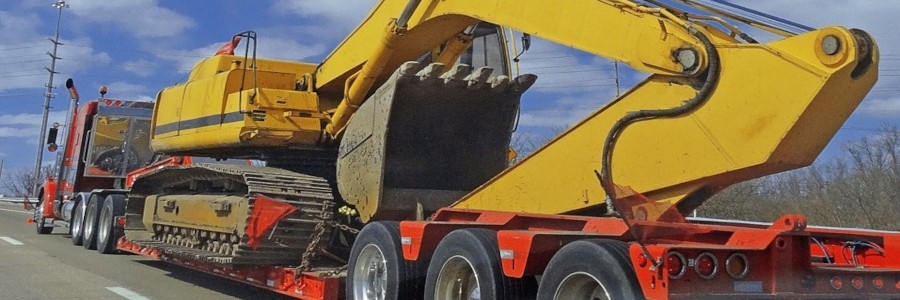
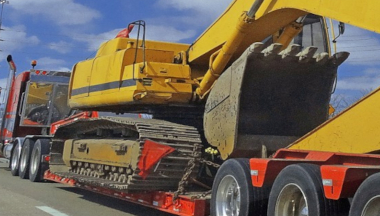
Ever since we introduced our ultra-low ash Delo® 600 ADF, proven to reduce ash buildup in diesel particulate filters (DPFs) by 60%, we’ve heard a recurring question: how do we manage to meet the performance requirements of a CK-4 heavy duty oil after removing the additive components that produce non-combustible ash? Metallic additives in oil are the largest contributor to unburned ash accumulation in DPFs, but those additives are there to help protect against wear and deposits. So, are we compromising performance by taking the “good stuff” out?
First, let’s be clear: we could not have brought this product to market were we not able to meet or exceed exacting API specifications for wear protection, oxidation stability and deposit control. Performance requirements are the top criteria that guide our formulating decisions. Years of R&D, exhaustive testing and real-world experience have shown that Delo 600 ADF meets and, on some measures, exceeds the performance of premium CK-4 oils.
We undertook the challenge to develop a lubricant that would minimize ash accumulation in DPFs, which robs engines of fuel economy, creates maintenance problems, and in the worst case can damage the engine and the aftertreatment system. We started by looking at the chemical “box,” or limits on the amount of sulfated ash, phosphorous and sulfur (SAPS) that an oil can contain. For sulfated ash, the maximum allowed content is 1% – and the majority of diesel oils on the market use that entire allowance of 1% or just slightly less.
Our formulation journey started by challenging the assumption that we needed to use that full “budget” of sulfated ash content to build a robust oil product. We set out to determine how little we could use and still meet the performance requirements. Sulfated ash in an oil is a reflection of the metallic componentry traditionally used in additive formulations, such as calcium and magnesium, zinc dithiophosphate and others. We began removing those components incrementally to see what the effect would be. The challenge then became to add back in the protective properties using componentry that does not contribute to sulfated ash.
This experimentation took place over several years, during which time engine technology evolved and performance requirements constantly changed. Through trial and error, combined with formulation knowledge that extends beyond the diesel realm, we ultimately refortified the oil with non-metallic or ashless components that deliver all the required performance benefits without the downside of unburned ash. The fact that ash is non-combustible is what causes it to accumulate in the exhaust filtering system. The components we employ in Delo ADF 600 are more combustible – they simply burn better than traditional metallic components.
It’s important to note that the additive system is not the only factor in producing the results we were after. Base oil selection very much played a role as well. By marrying the right base oil properties with our new additive chemistry, we were able to bring the sulfated ash content down to just .4% and still meet the performance requirements.
The story of Delo 600 ADF, then, is not about “taking stuff out,” but rethinking and reconstituting lubricant formulation to solve a real problem that has plagued our commercial customers. Our solution ultimately supports the goals of reducing emissions and controlling fuel consumption, without giving up any of the protection and performance that our customers expect from a premium heavy duty engine oil.
06/21/2021