A Better Way to Reduce DPF Clogging
Delo® 600 ADF
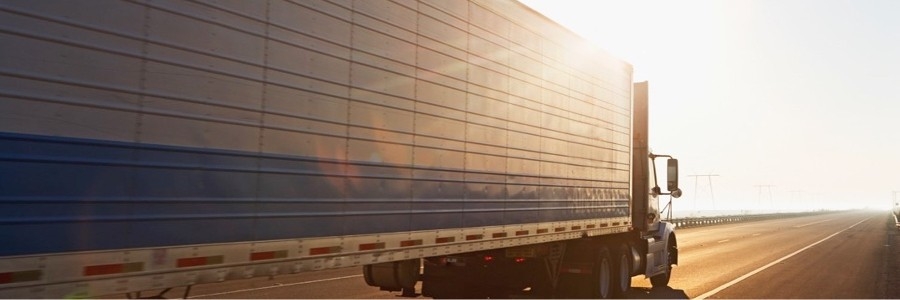
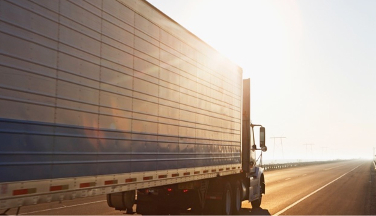
Diesel particulate filters (DPFs) are unquestionably efficient and effective at doing what they are supposed to do, namely reducing harmful emissions from heavy duty diesel engines. However, the buildup of non-combustible ash in DPFs clogs the filters, impairing their performance and reducing their efficiency. Left unchecked for too long, DPF clogging can also impair engine performance and diminish fuel economy. That is why they require periodic cleaning, which is a maintenance headache for fleet operators. First, it is a costly and laborious process, usually involving a chemical treatment to break down the ash and special equipment to blow it out of the filter. What’s worse, it requires taking a truck out of service for as much as a day, meaning downtime and lost revenue.
The main causes of ash formation in DPFs are the metallic additives in heavy duty engine oils, whose formulations typically include calcium, magnesium, zinc, phosphorus, molybdenum and boron. To help minimize the accumulation of ash and the resulting maintenance requirements (and costs), Chevron developed the first diesel oil based on a new, patented ultra-low ash (ULA) technology. Delo® 600 ADF is formulated with a novel additive package that has proven in exhaustive testing to be just as effective at wear protection, oxidation stability and oil life extension as conventional additives. More significantly, ULA technology reduces the ash content in the oil from the API-mandated maximum of 1% (considered “low ash”) to just 0.4%. This 60% reduction in ash content dramatically slows the buildup of ash in the DPF, meaning longer and more predictable maintenance intervals, while delivering a fuel economy benefit as well.
It has been suggested that operators can slow down DPF ash accumulation with a conventional, 1% ash CK-4 oil simply by reducing oil consumption in the engine. One can see the logic in this argument – the less oil consumed, the less unburned ash flowing out through the exhaust aftertreatment system. And reducing oil consumption without compromising lubrication and protection is always a desirable goal.
But as a practical matter, how do you actually control oil consumption? It’s not as though there is a dial on the dashboard that you can turn up and down to regulate the flow of oil. This logic relies entirely on the ability of an oil to inhibit piston deposit formation in the power cylinder, which is the main driver of increased oil consumption over the life of an engine. In other words, the rate of oil consumption depends largely on the properties of the oil being used, and is otherwise out of the operator’s control.
On the other hand, the selection of an ultra-low ash oil is very much within the operator’s control and effectively guarantees minimal ash accumulation, making it a much easier and more predictable solution. By the way, our testing of Delo 600 ADF found that it also exhibits remarkably good piston deposit control – so it will help limit oil consumption along with the specific and unique additional benefit of limiting ash buildup in the DPF.
How much of a difference can a ULA oil make over the long haul? The most commonly used metric for oil consumption is miles traveled per quart of oil consumed. That figure is bound to vary widely from one engine to another, and oil consumption generally scales in proportion to fuel consumption. If an engine is working harder and burns more fuel, it will simultaneously consume more oil.
Let’s assume, however, an average oil consumption rate of 4,000 miles per quart. It might be much less in an older engine and far more in a brand new engine, but that is a good starting point. After 400,000 miles, the engine will have consumed 100 quarts or 25 gallons of oil that pushes unburned ash through the exhaust system and into the DPF. Now consider whether all that oil has a 1% or a 0.4% sulfur ash content. Simple math tells us that an ultra-low ash oil is going to produce a fraction of the ash accumulation of a low-ash CK-4 oil.
Certainly the lubrication industry as a whole has made tremendous progress in ash reduction over the past decade. The CK-4 standard represented a huge leap over previous generations. Now, the introduction of ULA technology is a game-changing breakthrough, achieved without compromising any of the protective benefits you expect from a CK-4 oil. Simply stated, if you really want to minimize DPF ash accumulation and avoid unpredictable maintenance and downtime, then you are better off with an oil specifically designed for that purpose. And at the time of this posting, there is only one on the market.
05/24/2021