Why Proper Coolant Maintenance Matters
Check your coolant when you check your oil
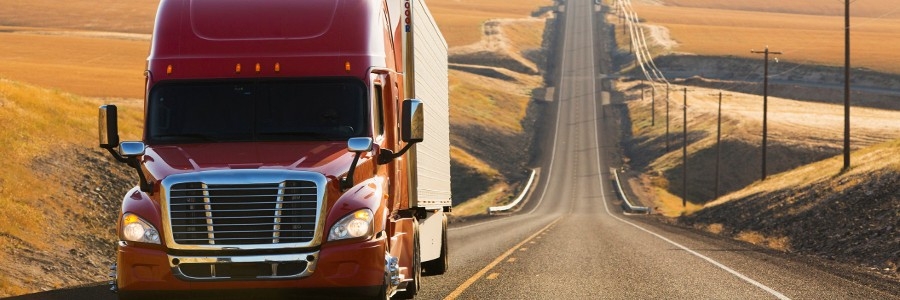
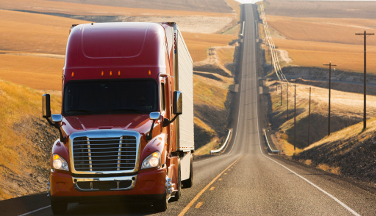
Heavy duty engine coolants are one of those things you might not think about as long as they’re working properly – until you have an overheating problem. By then, it’s probably too late to take the measures necessary to prevent the problem in the first place. Of course, you should follow the OEM’s recommendations in the choice of coolants for the vehicles in your fleet, as well as its maintenance requirements. But best practices in coolant system management suggest going above and beyond the basics.
Fleet maintenance managers are usually diligent about preventive maintenance with their engine oils – for example, pulling samples and running analyses for particle contamination or degradation. But coolants don’t always get that level of attention. They should. One way to implement a routine coolant preventive maintenance program is to schedule checks at the same time as your regular oil checks. Use a refractometer to check the coolant’s freeze point, and check the pH levels as well to make sure both are within acceptable limits. If they’re not, it could be an indicator of a deeper problem that requires pulling a sample and doing a thorough analysis. Also check to see if the coolant needs topping off. Some evaporation is to be expected, but a big drop in the coolant level may be an indication of a leak in the cooling system. Finally, pressure test the system to make sure the radiator cap is functioning properly.
It’s not uncommon for fleet shops to have several coolants in stock, especially if the fleet has a mix of engine types from different OEMs. One OEM may require coolants containing nitrites while another may specify nitrite-free products. This adds to the complexity of managing coolants and is another reason to have an ongoing and robust preventive maintenance program.
Coolants have become quite sophisticated in their chemistry as they have evolved. In the early days of trucking, just air and water were used to try and keep engines cool. But air cooling alone required too much power to run fans to prevent overheating. And water was problematic in areas where the winter temperatures dropped below water’s freezing point, not to mention the risk of rust and corrosion. Adding glycol to water enabled coolants to operate in a wider range of temperatures, while inhibitors were added to help prevent problems with rust. Over the years, inorganic additives such as phosphates and silicates were introduced to help prevent corrosion by adding a protective layer over all metal surfaces. However, these additives tended to deplete quickly, leading to a relatively short service life for the coolant. That led to the development of organic acid technology inhibitors, or OATs, which target only those areas where corrosion is beginning to occur. Today, the life of a coolant with OATs can be as much as one million miles, or even more when treated with an extender.
Coolants today also do much more than simply prevent overheating. For instance, modern engines have been designed to meet strict emission standards with exhaust after-treatment systems that include exhaust gas recirculating (EGR). In order to do its job, the EGR has to reduce the exhaust temperature, which contributes to more efficient combustion in the engine, and that in turn reduces nitrogen oxide and particulate matter in the exhaust. In order for the EGR to do that, it needs to be able to cool the exhaust gases. Diesel engine coolant is generally used to cool the EGR before it recirculates the exhaust back into the engine.
This simply underscores the need to make sure your coolants are maintaining the proper chemical balance and not degrading. Routine preventive maintenance checks will help prevent problems not only with cooling systems, but with all the engine and exhaust system components that rely on coolants for proper functioning.
05/14/2021