Used oil analysis: Proper sampling produces more reliable results
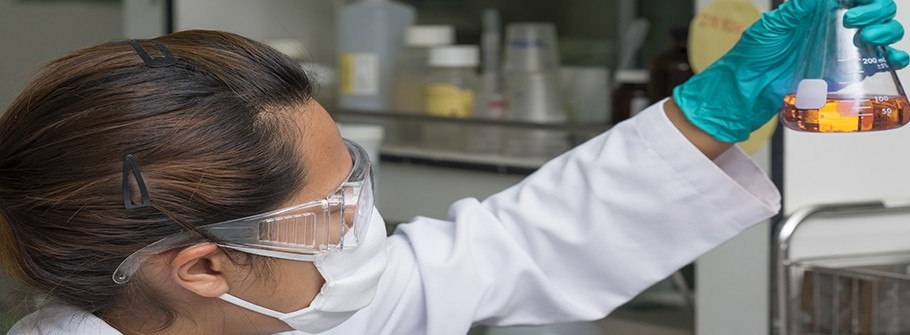
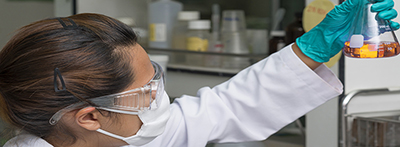
Whether you are operating heavy duty on- or off-road vehicles or fixed industrial equipment, it pays to have a used oil analysis performed routinely by a specialized lab. Checking the oil that’s flowing through your equipment for contaminants and general stability helps you determine appropriate drain intervals and helps protect your equipment by uncovering the causes of wear. For instance, if the analysis turns up excessive levels of dirt, iron, aluminum or chrome, you could have an air leak, or perhaps you need a new filter or breather. A used oil analysis will give you an indication of the issues you need to address to protect your equipment.
In North America, Chevron contracts with two independent labs for routine oil testing, and we put them through a rigorous vetting process. Many of our customers work directly with labs of their own choosing. Some larger companies even invest in their own testing facilities – the so-called “lab in a box.” Regardless of who does the analysis, getting results you can act on starts with proper sampling.
Collecting oil samples is not as easy as it sounds, and companies need to recognize the importance of good sampling practices. The lab is going to be looking at particles of less than 10 microns in size. If particles in the air, or from external sources, get into your sample after you’ve taken it, which can easily happen, it will skew your results. Following a few simple steps can ensure you get a good, clean sample that is representative of the oil in your system.
Take samples consistently from the same spot. It’s best to sample from an active stream in the system, while the equipment is running and the oil is fairly warm. What’s most important, however, is sampling from the same place consistently. Otherwise, you might see widely-varying results from one analysis to the next.
Take samples at regular intervals. If you wait too long between samples – say 1,000 hours versus 100 – you are bound to see signs of wear that appear abnormal. Sample often enough and regularly so the lab can establish a good baseline to monitor change in your system.
Never sample from the drain pan. Some people think it’s the easiest place to take a sample, when in fact it is full of contaminants from earlier drains and debris around the drain plug.
Use a clean, dry bottle. Don’t open the bottle until you’re ready to take the sample. Make sure it is clean and seal it quickly once you have the sample. You’re probably only taking around 4 ozs. to represent a reservoir holding hundreds or even thousands of gallons of oil. The lab will use only a fraction of that for each of the many tests it performs.
Don’t fill the bottle to the top. Leave a little room in the bottle so the lab technician can shake it up to disperse particles that have collected at the bottom.
Label the sample accurately and thoroughly. Be sure to identify the exact oil viscosity or SAE grade in addition to the brand and product name. Show the type of equipment, the number of hours on the unit and the hours since the last oil change as well. Identify the equipment with the exact same nomenclature each time – otherwise, the computer will think it’s a different piece of equipment and start a new database. The more accurate information you give the lab, the more precise an analysis they can give you.
Assign a designated sampler. Ideally, you will have one person who becomes familiar with the process to ensure consistency.
Send it in quickly. Don’t leave samples sitting on a shelf until the end of the year. Send them immediately, and then check the results when you get them.
Regular used oil analysis can help you extend equipment life and optimize lubricant life, avoid unforeseen breakdowns and reduce your maintenance costs. Providing clean and consistent samples to your lab will produce results that tell you what you need to know.
03/23/2017