Simple solutions for meeting equipment manufacturer’s oil cleanliness specifications part 1: Start clean
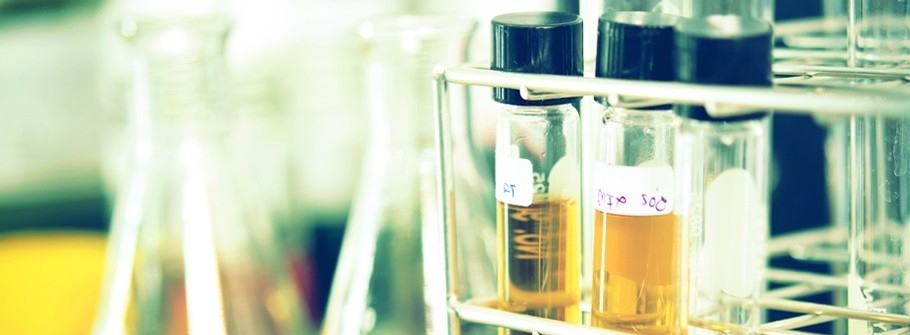
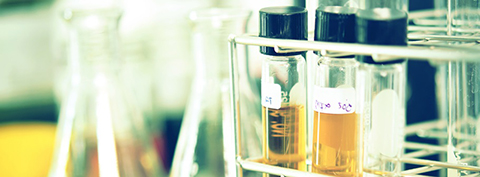
This is the first of a three-part series discussing the phases of an effective lubricant cleanliness program: Start Clean, Monitor and Stay Clean.
Particle contamination is the number-one cause of lubricant-related equipment failure. Dirt particulates, moisture, varnish and gases are the primary examples of contaminants that, if left unchecked at unsafe levels, can cause damage to the very equipment the lubricant is intended to protect. These contaminants can also reduce the performance of the lubricant and many times shorten the intended life of the lubricant. From mobile equipment in construction and waste collection to fixed equipment in manufacturing and power generation plants, any enterprise that depends on the reliable operation of heavy duty equipment needs a systematic approach to maintaining lubricant cleanliness at levels specified by the equipment manufacturers.
First, start with a baseline assessment on the cleanliness of the new oil at your facility. This entails working with your lubricant supplier and performing a simple site assessment at your facility. Pull samples from your bulk oil storage and have them analyzed by an oil analysis laboratory. Make sure to include particle count analysis (ISO 4406-99). You can also have a simple onsite visual analysis performed by a lubricant field engineer via a patch test analysis.
Once you know the baseline cleanliness of the new oil stored at your facility, research the oil cleanliness requirements of your equipment manufactures and compare. Armed with this information, you can set a cleanliness level standard with your lubricant supplier for new oil delivered to your facility. If you have multiple types of equipment, it’s advisable to focus on the equipment and/or component with the lowest machine clearance level and use this as your target cleanliness level. Prior to setting your target cleanliness level for each lubricant product it is extremely important to consult with the lubricant manufacturer to ensure each product can handle the level of filtration required to meet the target cleanliness level.
With this initial research done, the site assessment should include the review of various areas to ensure you are truly “starting clean.”
Observe Lubricant handling and storage practices. Watch the process you have for transferring oil into equipment, and look for ways to mitigate the risk of contamination at any step in the process.
- Evaluate vulnerability to air contamination. One important aspect to look at is air management and the breathers that control the flow of air into and out of oil tanks. A good quality breather will be able to filter air down to three microns of particulate matter or less, which is an appropriate target to start with for air management.
- Check the fill openings. Do you have conventional flip caps on oil tanks? Replace with a stronger seal cap, such as a pressure prevent cap. Consider using cam-locks for sealed connections when new oil is delivered into storage tanks, rather than simply sticking a nozzle into the opening. It is also a good best practice to have secondary filtration at the dispensing point, usually an in-line filter just behind the filling nozzle. You wouldn’t want to rely on a secondary filter to meet your cleanliness targets, but it is an effective way to mitigate contamination that may have occurred during the transfer process or from a possible pump failure.
- Examine the condition of lubricant storage tanks. If there is rust inside the top of a tank, the tank should be replaced. If unacceptable levels of contamination are present, the best option is to have the tank cleaned out or replaced. If this is not an option the next alternative is to simply start filling the tank with oil that meets your cleanliness targets, and over time the contamination can be reduced to acceptable levels.
All that said, the key to starting clean is to ensure that your marketer is delivering lubricants that are certified to meet your equipment manufactures oil cleanliness specifications. Relying on filtration at your facility to meet cleanliness targets can be very expensive, labor intensive, and increase the risk of damaging the lubricant by over-filtering. It’s more cost-effective to start with a product that meets your target in the first place and is backed by the lubricant manufacturer. Chevron’s new ISOCLEAN® Certified Lubricants are a simple solution to get you started clean. From there, it’s a matter of managing your handling process so that the lubricants stay within your cleanliness targets. Over the next two articles, we’ll cover how to sustain a cleanliness program once the basics are in place.
01/06/2017