Interpreting oil analysis: What does it tell you?
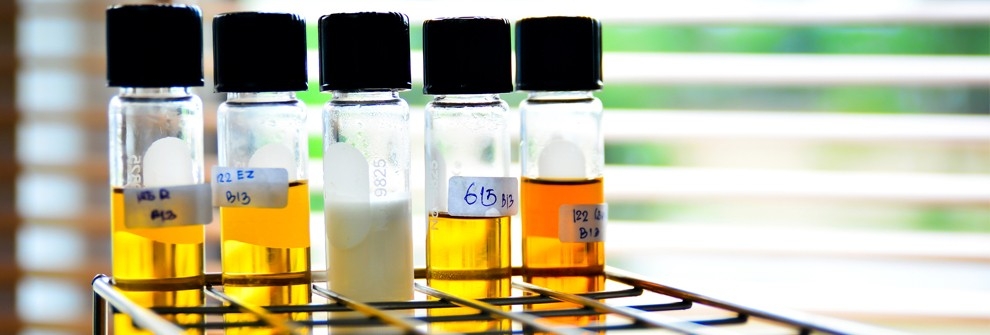
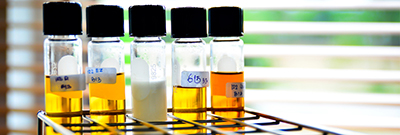
We’ve written quite extensively on the benefits of oil analysis and the proper methods of sampling oil for testing. Many of our customers know from experience that a routine laboratory analysis of in-service oil can help predict and prevent equipment failure or maintenance issues caused by oil contaminants.
But what exactly does an oil analysis tell you? What kind of information does it yield? The main things are the types and levels of contaminants in the oil itself, the possible causes of contamination, and indicators of equipment wear that warrant further investigation. In its report, the lab will flag areas of concern using either a 1-4 ranking or a green, yellow and red light system, red indicating an area that needs immediate attention.
One important indicator the lab looks at is oil viscosity. Operating conditions can actually change an oil’s viscosity from the grade on the label. For mobile equipment, engine, transmission and gear oils are measured at 100oC. In industrial applications, the oil is measured at 40oC. If the viscosity is either much higher or much lower than the original, it’s a sign that the oil is breaking down, thickening, oxidized or cross-contaminated with another product – in all cases, requiring change right away.
The lab will also look at the additives in engine oils, such as zinc, phosphorous, calcium and magnesium. If parts per million (PPM) levels are consistent, it’s a good sign the oil is not experiencing cross-contamination.
The presence of wear metals, such as iron, copper or tin, provides evidence of equipment wear. If the metal particles are increasing in number, it’s possible that excessive wear is taking place and the equipment from which the sample came needs to be inspected closely.
The analysis will tell whether the oil has experienced excessive water contamination. The lab may also look at the acid and base numbers. Acid levels indicate the extent to which the oil is overheating or oxidizing. The base number measures the alkaline reserves in the oil, which offset the acid and help prevent corrosion. If the acid number is too high or the base is too low, the oil needs to be changed.
An oil analysis can also detect a coolant leak within the engine. Water or glycol may vaporize as soon as they leave the cooling system, but coolant contaminants may leave traces of sodium, potassium or boron in the oil, which are indicators of a coolant leak.
Levels of silicon and aluminum, the basic components of dirt, are clear indicators of an air intake filtration leak letting dirt into the combustion chamber. High levels of chromium suggest that the resulting abrasion is wearing chrome off the piston rings.
Some level of contamination is bound to occur. The question the lab will answer is whether the levels are within the limits of tolerance for the particular application. That is why proper and detailed identification of the sample including oil brand, grade, hours on oil and equipment, application and filtration are so important. The lab’s report may include recommendations to check certain aspects of the equipment, such as the air intake system or wear items that may explain abnormalities in the oil. Armed with this information, you are better prepared to take preventive action to protect your equipment, extend its useful life, minimize downtime and avoid premature replacement costs.
01/11/2018