Check the third spec: Don’t assume new oil is clean
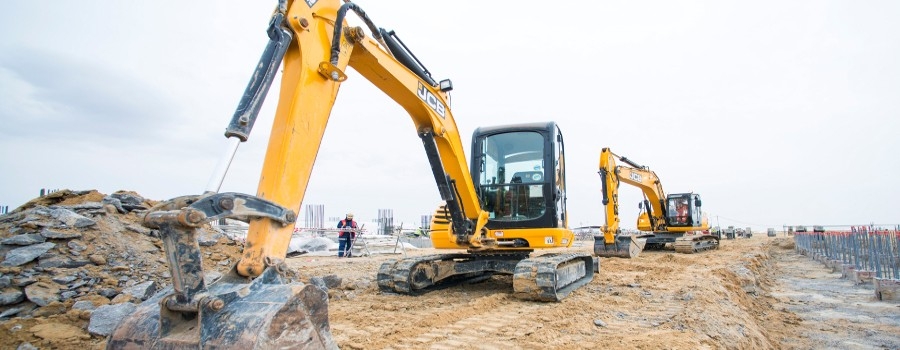
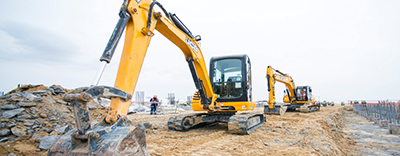
Equipment operators generally assume that when they take delivery of a lubricant, it is going to meet the OEM’s performance and viscosity specifications for their applications. And those specs are certainly important. But they often overlook an equally important specification: the OEM’s lubricant cleanliness requirement, as expressed in the ISO cleanliness code. They may assume if an oil is new, it must be clean. But new doesn’t always mean clean. In fact, more often than not, new oils fall short of the OEM’s cleanliness spec.
There are many opportunities along the oil transportation route for particulate contamination to occur - from the base oil plant, to the end-user’s bulk tank, as well as a site’s lubricant maintenance activities. The bottom line is, if the oil is not protected during the journey, more than likely it will not meet the OEM’s preference for ultra clean oil. Which is why it should not be a surprise that the number one lubricant-related failure is high levels of contamination. A leading OEM has shared 82% of the reason hydraulic equipment fails prematurely is due to contamination. Extremely small particles (invisible to the naked eye) can cause severe damage and shorten component life. Any operation using hydraulic equipment has probably experienced a blown hydraulic hose. A 2016 study from Parker found the primary cause of a blown hose was tube erosion resulting from the steady flow of tiny, abrasive contaminants.
What is the cost to our business of having to repair or replace a critical piece of equipment?
Let’s look at a single hydraulic hose failure for a construction company. When you total up
the replacement part, lubricant loss, maintenance labor and downtime, a single failure costs
around $920. If you apply this example across an organization, a conservative estimate of
needing to replace 50 hoses over the course of a year would total $45,000 annually.
Thus, it makes sense than companies may try to make improvements, such as filter their oil. However, this strategy can be costly and risky. Depending on a system’s flow rate, tolerances, temperatures, initial contamination level, load and/or pressure, their attempts to correct could be flawed. For example, if using too tight of a filter, less than 10 microns for example, there is a significant risk of pulling out anti-foam. Not all oils are easily filterable, and by not understanding a finished lubricants formulation, there is a risk of taking out an important lubricating property which may result in more damage in the long-run. Also, when adding additional filtration, whether it be a kidney loop or on-line system, there are costs to operating, maintaining and having the man-power to run the system. With production demands and other business pressures, is filtering your oil the most efficient use of your time? Another risk with on-board filtration is the time it takes to get the oil clean, in which damage is likely occurring during that filter system’s clean-up time.
Chevron has long advocated a systematic oil cleanliness program that includes establishing your maintenance program baseline with a no-cost site assessment of your key lubricants on site. Key program components include a review of the maintenance team’s lubricant handling practices, sampling procedures, laboratory testing and setting the appropriate ISO Cleanliness goals for your operation. Once you understand your OEM cleanliness specifications and the current baseline, you can make smart decisions about where to spend time and money to effectively mitigate the issue. Operators who take proactive measures will see tangible benefits in the form of longer equipment life, reduced downtime and lower maintenance costs. You can also avoid keeping idle, non-productive equipment on a work site “just in case” a piece of equipment breaks down.
In today’s day and age, we talk about preventative health care as the best path forward for a long and fruitful life. The same holds true for your equipment. Starting with certified clean oil provides reassurance that you are being proactive to maintain your equipment for the long-run. And be sure to monitor the health of your equipment with used-oil analysis. You’ll be amazed to see the wear rates drop once you are operating within the OEM’s parameters of clean oil.
06/27/2019