Buy In to Buy-In
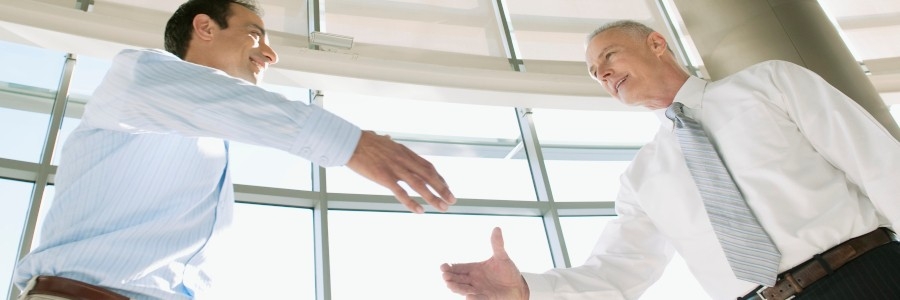
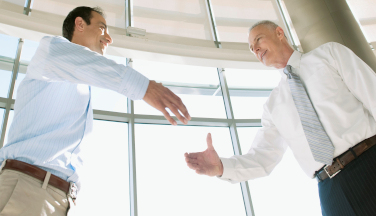
The task of building a new reliability program from the ground up can be daunting. The first obvious hurdle is universal across every industry: budget. It’s easy to envision overhauling your program with shiny, new equipment and get swept up reading the brochure for the Oil Perfection 500 (*not a real product), thinking about how your program would be perfect if you had one. However, getting the funds to invest in your program might be easier than the true investment that pays dividends—buy-in from your technicians, your site leadership and your corporation.
Overhauling your policies and procedures on a program as large as lubrication is no small feat. Especially in facilities that have long-tenured team members, it can be difficult to change the way the company operates. Skilled maintenance personnel fall into their routines and they rely on what they know. It can be difficult to convince them change is better. For some, it might seem outright impossible to convince them there’s a better way to complete a task. So, what are some ways to build your program with buy-in? Start by looking at ways to make doing the best practice the easiest practice.
- Upgraded sight glasses allow technicians to read the oil level without having to open the system to check a dipstick. This task can be done at a greater distance which eliminates the need for ladders or a tie-off to access hard-to-reach locations. While checking a dipstick may only take 45 seconds, reading a clean, clear sight glass may only take 5 seconds.
- Advanced desiccant breathers and quick connect fittings for filling and draining reservoirs dramatically reduce the ingress of contamination into equipment. This in turn increases the life of the equipment, allowing it to run longer. As the mean time between failure increases, the amount of wrench-time needed for that machine center goes down.
- Using Chevron’s ISOCLEAN® Certified Lubricants guarantees the oil you’re bringing into your facility is at the cleanliness level you require. Typical oil may not meet the OEM’s cleanliness specification, so many companies rely on onsite filtration to reach the desired cleanliness level. There are risks of filtering the oil on your own, as well as the costs of labor to monitor the filter cart. Having pre-filtered oil arriving clean and ready for use is one less “to do” on an already over-stacked maintenance list.
The maintenance team is not the only group who need to embrace the changes needed to fulfill a goal of developing a precision lubrication program. Implementing plant-wide programs brings many voices to the table – maintenance managers, buyers and planners, operations leadership, the unit manager, etc. These roles aren’t going to be the boots on the floor, but their buy-in provides the structure and support for your program that is critical for it to succeed. Instead of focusing only on the costs of the program, focus your message on the returns for the program and how precision lubrication can pay for itself.
- PM work orders can be developed or updated to ensure lubrication points are clearly defined, making it easier to train new hires and reducing the risk of a mistake. This level of documentation is usually lacking in facilities just beginning their journey to precision lubrication, but good documentation leads to fewer costly mistakes on the floor such as the wrong oil being used.
- Using Chevron’s ISOCLEAN® Certified Lubricants makes it easier to maintain supply for emergency use. If you have a large hydraulic spill and need to fill up the reservoir to get it back up running, you don’t want to replenish your reservoir with dirty oil that hasn’t been filtered. This action can contaminate the system you’ve already invested money into cleaning.
- Reach out to industry experts and see what options are available to modify your equipment. Especially now that virtual meetings have become commonplace, it’s easy to scope out projects and improvements with outside support. This means less research required for a program manager to find solutions to lubrication issues. It can also provide more information for maintenance managers to decide the most efficient use of their budget.
The last group you want to look for buy-in from is the corporate gatekeepers. While corporate reliability teams may be primed to give support to a program, they’re often facing the same kind of budgetary constraints of a plant’s leadership.
- More reliability is more uptime. Corporate leadership is looking at the numbers. They want to see that overall machine uptime is improving, that the mean time between failure is becoming greater, and that the overall manpower required to maintain that machine is not increasing. Precision lubrication is directly related to machine life and machine life is directly related to how much manpower is required to maintain assets.
- Start with small improvements and program initiatives and wait to expand when you are doing those things well. This builds a solid foundation for the future of your program, and it allows you to document the improvements as you progress. Sharing these improvements with small, incremental spending gives more credence to a request for larger investments in the program.
- Chevron’s ISOCLEAN® Certified Lubricants help companies extend the life of their equipment. Eighty-two percent of equipment failure is due to contaminants in the oil. Starting with clean oil lowers the probability of the equipment failing. Longer running equipment means less maintenance costs or equipment turnover which means an improved bottom line. This should make corporate leadership very happy. As you build your program and begin to see some of the wins, make sure to document and share those victories. For your maintainers, those wins are a testament to their hard work. For your peers, those wins stem from their support of your initiatives. For the corporate gatekeepers, those wins are proof the precision lubrication program is adding value to your site and to the organization.
06/15/2023