Looking to Boost Operating Efficiency? Look at Your Hydraulic Fluid
Today’s hydraulic systems demand high-quality oils
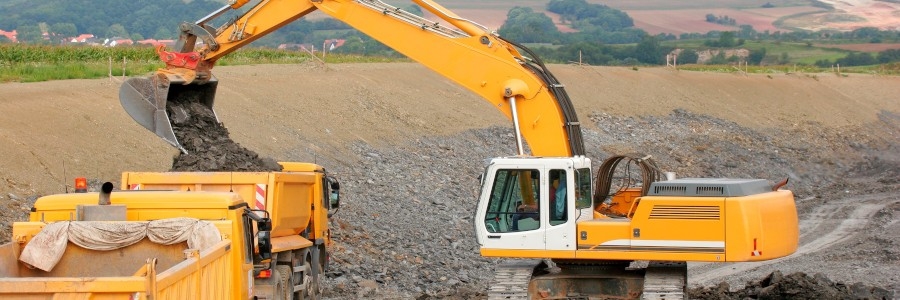
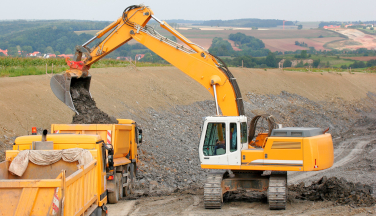
Between cost pressures and customer demands, industrial equipment operators are always looking for ways to optimize efficiency. Whether in equipment performance, process improvement or energy consumption, increased efficiency should translate to lower operating costs and higher productivity.
Today’s modern hydraulic systems are engineered to perform at higher speeds, under higher operating temperatures and more severe pressure than even just a few years ago. As a result, the choice of a hydraulic oil has a big influence on equipment performance, reliability and longevity. Moreover, selecting a high-quality hydraulic oil is an often-overlooked opportunity for significant, measurable efficiency gains that go straight to the bottom line. In exhaustive testing and real-world applications, using a premium hydraulic fluid has shown to help increase efficiency on a number of measures, including equipment reliability, energy savings, and the life of the oil itself, compared to a conventional fluid. Conversely, an underperforming oil can reduce volumetric flow, which then leads to reduced or delayed pressure in hydraulic systems, resulting in a costly drag on performance and productivity.
In field tests running a medium-sized excavator using both Clarity Synthetic Hydraulic Oil AW 46 and a traditional monograde hydraulic oil 46, the increase in productivity and fuel e efficiency can be estimated at approximately $9,000 in annual savings from a $300 investment in lubricant costs (actual savings will vary). To cite a specific field test example, the use of Chevron’s Clarity® Synthetic Hydraulic Oil in a Husky XL 300 plastic injection molding machine resulted in a 4.2% reduction in electricity consumption compared to a conventional monograde hydraulic fluid.
So what are the attributes to look for in a hydraulic fluid that indicate the potential to help improve efficiency in industrial machinery or construction equipment? In general terms, it is the balance of a premium base oil, the formulator’s unique additive chemistry, and fluid cleanliness that determines performance. These qualities vary, of course, from one lubricant producer to another – which makes it extremely difficult to compare oils strictly on the basis of their data sheets.
Lubrication and maintenance engineers often look at the Turbine (Oil) Oxidation Stability Test, or TOST, life as a basis of comparison, since that is one of the few common parameters among different oils. TOST life is certainly an important measure, indicating how long the oil has shown to withstand oxidation, but it is just one of many and is by no means definitive. TOST testing is complex, and could also be considered a misapplication of a test, depending on the application the fluid is going into (i.e. turbine vs hydraulic). It often has to be modified for today’s oils that are capable of lasting longer than the 10,000-hour standard (see our ashless line of Clarity Hydraulic for impressive TOST results).
Other properties, including low-temperature pour-point and fluidity, corrosion protection, and a stable viscosity index are key considerations in evaluating hydraulic oils. There’s a clear trend toward synthetics in industrial applications, which have the advantage of consistent performance across extreme hot or cold temperatures. The oil cleanliness factor should not be underestimated – microscopic particle contamination under pressure in hydraulics is a leading cause of equipment failure. Testing has shown that it also has an adverse impact on system pressure, which drains efficiency, impedes production, and accelerates wear. Using an oil that is certified clean to the OEM’s ISO 4406 specification will help mitigate these effects and improve operating efficiency.
Bottom line, if you’re selecting a hydraulic oil primarily on price, you could end up paying a steeper price in the long run in the form of lost efficiency. A premium hydraulic lubricant will pay itself back many times over through tangible efficiency gains and reliable equipment performance.
Chevron offers a complete line of premium hydraulic lubricants, including Clarity Synthetic and Rando® HDZ, proven to increase overall operating efficiency,when delivered to your OEM’s ISO 4406 specifications. Contact your Chevron rep or lubricant marketer to learn more.
01/25/2022