More Complex Aftertreatment Systems Require Rethinking Oil Formulations
Fleets will need to extend DPFs as long as possible
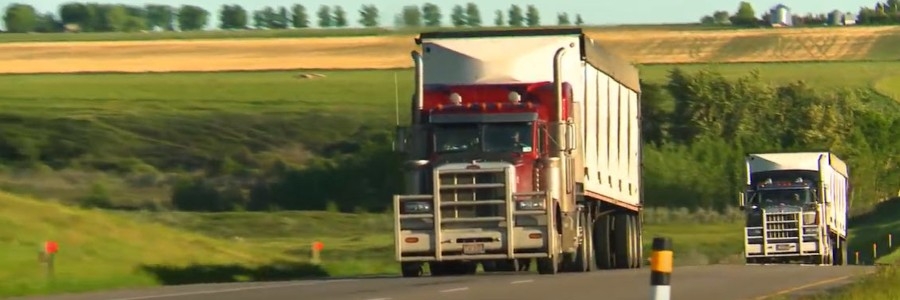
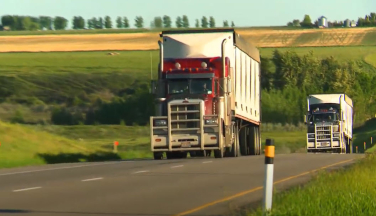
There was a time when diesel engine oil formulators’ primary concern was simply protecting the engine. However, as EPA emission control regulations came into force, heavy duty OEMs began to develop sophisticated exhaust aftertreatment systems (EATS) in an effort to reduce nitrogen oxide (NOx) and particulate matter (PM) emissions. Oil formulators had to account for these new components, but initially that meant doing as little harm to them as possible. That is what led, for example, to the 1% ash limit in the API CJ-4 and CK-4 generations of engine oils, which are formulated to help control the buildup of unburned ash in the EATS.
Over the years, clean air standards have become increasingly stringent, and as a result, aftertreatment systems have become increasingly complex. A typical aftertreatment system today likely includes a diesel oxidation catalyst (DOC), a diesel particulate filter (DPF), diesel exhaust fluid injection (DEF) to decompose NOx, a selective catalytic reduction (SCR) system, and possibly an exhaust gas recirculation (EGR) system.
And now, more stringent regulation is on the horizon. The California Air Resources Board (CARB) Omnibus Regulation for heavy duty engines and vehicles mandates that OEMs must develop more effective and durable aftertreatment technologies. The rule calls for an initial 75% NOx reductions and 50% particulate matter reductions starting with model year 2024, with even more aggressive targets starting in 2027. Coinciding with these more rigorous standards, the API has approved the creation of two new engine oil categories, under the banner of Proposed Category or PC-12, to replace CK-4 and FA-4 oils by 2027. Among many other requirements, support for new aftertreatment technologies is a priority of the PC-12 initiative.
For lubricant formulators like Chevron, the implications are clear. We can no longer think of the aftertreatment system as something in the background that we can design around. Rather, we must look at the engine and the EATS as a whole, and formulate lubricants that will protect both components.
DPFs take the brunt of punishment from today’s hotter-running engines. Ash and soot accumulation clogs the filters, which is a drag on engine performance and fuel efficiency – and a maintenance headache for fleet operators. Trucks have to be taken out of service in order to clean the DPF, or moved to the side of the road to perform a forced regeneration, accelerating the engine to high temperatures to burn off soot. Some OEMs are now recommending that operators clean the DPF only once, then replace it when the ash accumulation returns to the point that it would require another cleaning.
The problem with that approach is that global demand for DPFs is skyrocketing. Europe’s latest emission standards will virtually require DPFs in all off-road diesel equipment. China and India, who together produce around 1.5 million heavy duty trucks a year, have introduced standards that will require DPFs in all on- and off-highway diesel-powered vehicles. Combine that with the fact that much of the precious metal needed to fabricate DPFs comes from Russia, and we have a very unstable supply chain issue that makes DPFs more difficult to acquire.
It is clearly in a fleet operator’s best interest to extend DPF life as long as possible while trying to minimize maintenance and regens. That brings us back to the role engine oil formulators need to play in protecting aftertreatment systems. The majority of the ash buildup in the DPF is attributable to non-combustible additives in the engine oil. Reducing the sulfated ash content in the engine oil can help prolong DPF service life and extend maintenance intervals. In 2019, Chevron launched Delo® 600 ADF specifically to meet that need, leveraging our patented ultra-low ash (ULA) technology to reduce ash by 60% compared to conventional CK-4 oils, and dramatically slow down the buildup of ash in DPFs. Delo 600 ADF is proven to reduce DPF maintenance requirements and restore lost fuel economy.
Cleaner air benefits everyone, and we must all do our part to help meet emission goals, however aggressive they become. Lubricant producers have a particular responsibility to keep up with engine technology and help ensure that today’s complex aftertreatment systems do what they are intended to do: reduce harmful emissions.
12/01/2022