Webinar: How to build a modern maintenance shop for small and medium-size fleets
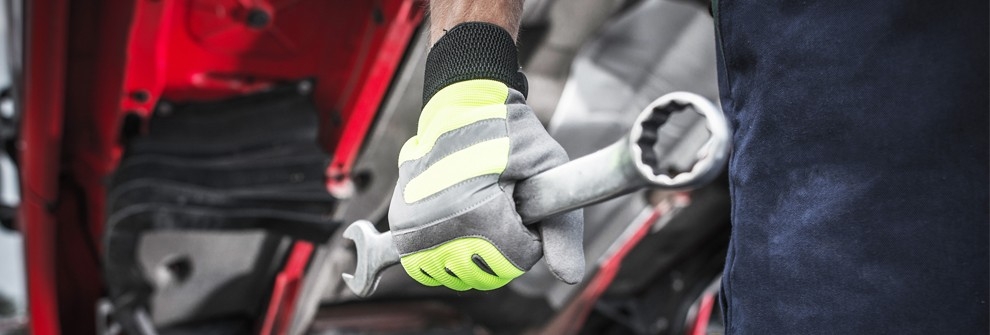
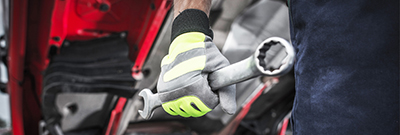
Truck technology is changing, labor costs are rising, and the pool of skilled technicians is shrinking. Are your maintenance facilities and practices keeping up with these changes?
This past February, Chevron teamed up with Fleet Owner magazine to host an online webinar, “How to Build a Modern Maintenance Shop,” geared to small and medium-size fleet operators. We had the privilege of having two distinguished industry experts on our panel: Glen McDonald, Director of Maintenance for Ozark Motor Lines in Memphis, and until recently the Chairman of the ATA’s Technology and Maintenance Council (TMC); and Darry Stewart, also a former TMC Chairman and now CEO of DWS Fleet Management Services in Wrentham, Mass.
Whether you are looking to refurbish an existing maintenance facility or build a new one from scratch, Glen and Darry painted a vivid picture of the things you need to consider. They traded tips on a wide range of issues: from safety and OSHA compliance to painting and lighting, how to optimize floor space, and how to organize parts and tools for fast and easy access. They repeatedly emphasized the need for a clean, bright and well-organized environment that technicians want to work in and that allows them to be their most productive.
Three key themes emerged from the webinar:
One, labor costs will be a key driver of your decisions as to how you set up your shop. Figuring that the average cost of labor is about $1 per minute, everything you can do to avoid wasted time and motion will optimize efficiency and deliver the most value per dollar.
Two, the technician shortage is real. Your fleet maintenance operations are competing with original equipment dealers and luxury car dealerships for a shrinking pool of talent. So it is important to create a work environment that attracts and retains skilled technicians and mechanics.
And three, it’s imperative to keep up with technology. Advancements like onboard ECUs, telematics and remote diagnostics help technicians take better care of trucks, but you need a computer in virtually every bay – and not a second-hand laptop, but the latest hardware and software.
On a topic near and dear to our hearts, Glen pointed out that with today’s oils and extended drain capabilities, shops that used to do as many as eight oil changes per vehicle per year are now doing no more than two. So valuable floor space for pits that used to be dedicated to oil changes can now be repurposed.
Chevron is actively working with small and medium-size fleet owners to help improve maintenance efficiency. If you weren’t able to attend our webinar in person, watch the recording. It’s a small investment of time that could pay big dividends in productivity gains down the road.
04/18/2018